Series 2A 109 inch 6 cylinder bulkheads 1967 to 1971
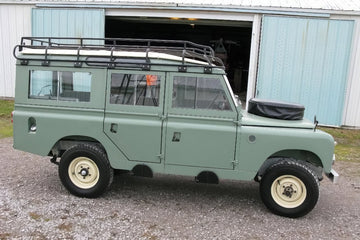
Production Dates
1967 To 1971 - Series 2A 6-cylinder Bulkheads
Over the course of production, The Rover Co. engineers made multiple incremental improvements to their bulkheads, but only ever used two Part Numbers, so Pegasus has introduced ‘Type’ numbers designed to easily identify which bulkhead you require, based on your vehicles production date.
The dates are provisional and are based on actual production dates. The Vehicle Registration date is no guide to the Build Date.
Unlike Series 2a, 4-cylinder bulkheads, Pegasus Bulkheads manufacture and supply the 6-cylinder bulkhead in ‘handed’ configuration, i.e. supplied pre-fitted with the correct Toe Plates and Cover Plates.
Toe Plates and Cover Plates are supplied loose to enable surface treatment and painting of all faces.
Follow our steps below to identify your bulkhead.
345611 (TYPE 6) LHD - Bulkhead, Series 2a, 6-cylinder, ROW LHD models, 1967 to December 1968
345611 (TYPE 6) RHD - Bulkhead, Series 2a, 6-cylinder, RHD models, 1967 to December 1968
345611 (TYPE 8) LHD - Bulkhead, Series 2a, 6-cylinder, LHD models, October 1969 onward
345611 (TYPE 8) RHD - Bulkhead, Series 2a, 6-cylinder, RHD models, October 1969 onward
348571 - Bulkhead, Series 2a, 6-cylinder NADA (Federal Specification) only
Handmade In The UK
Our Process
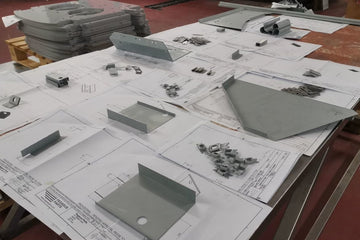
Individual Components
We utilize our own designs and patterns to cut and shape the final parts. We have invested in advanced tooling to create a bulkhead that is comparable to Rover's original engineering. Pegasus have extensive experience in sheet metal work and are able to replicate all original pressing details, holes, spire nut locations, and footwell ribs.
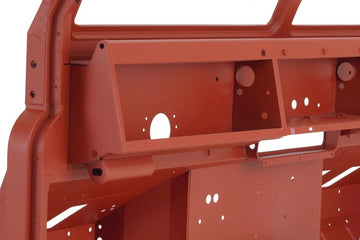
Made Stiffer, Stronger and Corrosion-free
Our parts are fabricated with minimal pressing, preserving metal thickness. Using modern design and materials, we have improved performance by strengthening and stiffening weak points by 50% compared to the original bulkhead. This means that not only does the bulkhead maintain its original appearance, but it is also more durable and long-lasting.

Spot Welded Like The Originals
Pegasus bulkheads are constructed using the same spot welding method as the original bulkheads. The majority of the parts are joined together using spot or TIG welding to create sub-assemblies, which are then assembled into the final assembly. To ensure precise bulkhead geometry, the assembly is constructed on a 36 reference point jigs.

Final Stage Welded
Pegasus utilize TIG welding on the final assembly for heavy-duty brackets, lap joints, and butt joints. The heavy-duty brackets such as the bonnet hinges, tie rod brackets, and bottom feet are also welded into place using TIG welding to replicate the original oxy-acetylene welding method. We maintain the highest standards in our manufacturing process and have complete control over the quality of each finished bulkhead.

Kind Words From Our Customers
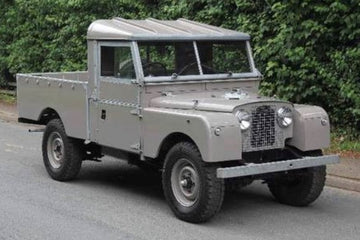
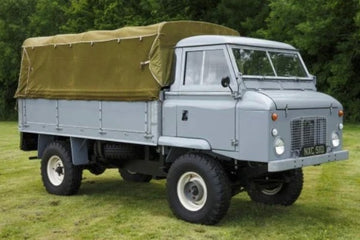
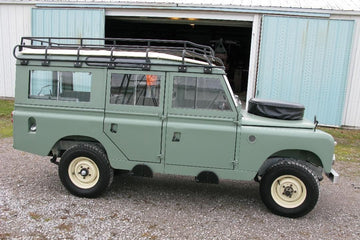
